The Scientific Research Behind Porosity: A Comprehensive Guide for Welders and Fabricators
Understanding the elaborate mechanisms behind porosity in welding is essential for welders and fabricators aiming for flawless craftsmanship. From the make-up of the base materials to the details of the welding process itself, a plethora of variables conspire to either exacerbate or minimize the existence of porosity.
Comprehending Porosity in Welding
FIRST SENTENCE:
Assessment of porosity in welding reveals crucial understandings into the stability and quality of the weld joint. Porosity, defined by the presence of tooth cavities or gaps within the weld steel, is a common problem in welding procedures. These spaces, if not correctly addressed, can compromise the architectural stability and mechanical residential properties of the weld, causing potential failings in the completed item.
To detect and quantify porosity, non-destructive screening techniques such as ultrasonic screening or X-ray evaluation are frequently utilized. These methods enable the recognition of internal flaws without compromising the stability of the weld. By evaluating the dimension, shape, and circulation of porosity within a weld, welders can make informed decisions to improve their welding processes and achieve sounder weld joints.

Aspects Affecting Porosity Development
The occurrence of porosity in welding is affected by a myriad of elements, ranging from gas protecting efficiency to the ins and outs of welding specification setups. One crucial factor adding to porosity formation is insufficient gas shielding. When the protecting gas, commonly argon or CO2, is not efficiently covering the weld pool, atmospheric gases like oxygen and nitrogen can pollute the molten metal, leading to porosity. In addition, the tidiness of the base products plays a significant duty. Pollutants such as corrosion, oil, or dampness can vaporize throughout welding, creating gas pockets within the weld. Welding criteria, consisting of voltage, existing, take a trip rate, and electrode kind, additionally influence porosity development. Utilizing inappropriate setups can generate too much spatter or heat input, which consequently can result in porosity. In addition, the welding method used, pop over to these guys such as gas steel arc welding (GMAW) or secured metal arc welding (SMAW), can influence porosity development because of variants in warm circulation and gas insurance coverage. Recognizing and controlling these factors are necessary for lessening porosity in welding procedures.
Effects of Porosity on Weld Top Quality
Porosity formation substantially endangers the structural integrity and mechanical buildings of bonded joints. When porosity exists in a weld, it develops spaces or dental caries within the product, minimizing the overall stamina of the joint. These voids serve as stress and basics anxiety focus points, making the weld more at risk to splitting and failing under lots. The existence of porosity likewise weakens the weld's resistance to rust, as the caught air or gases within deep spaces can respond with the surrounding setting, resulting in destruction over time. Furthermore, porosity can prevent the weld's capacity to endure stress or influence, more threatening the general quality and integrity of the welded structure. In critical applications such as aerospace, auto, or structural building and constructions, where safety and security and resilience are extremely important, the harmful impacts of porosity on weld quality can have severe repercussions, stressing the importance of reducing porosity through appropriate welding strategies and procedures.
Methods to Reduce Porosity
Additionally, using the appropriate welding parameters, such as the right voltage, present, and travel rate, is critical in protecting against porosity. Keeping a regular arc length and angle throughout welding likewise helps lower the probability of porosity.

Making use of the proper welding strategy, such as back-stepping or employing a weaving motion, can likewise assist distribute heat uniformly and lower the chances of porosity formation. By executing these techniques, welders can effectively lessen porosity and create top notch welded joints.
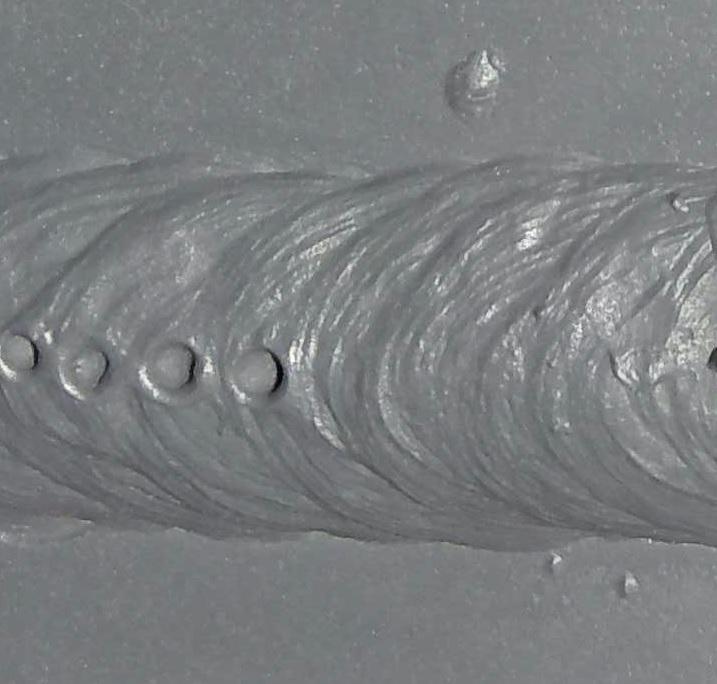
Advanced Solutions for Porosity Control
Implementing cutting-edge innovations and innovative techniques plays a crucial role in attaining premium control over porosity in welding procedures. One advanced option is using sophisticated gas combinations. Shielding gases like helium or a mixture of argon and hydrogen can aid reduce porosity by providing better arc security and boosted gas coverage. Furthermore, using advanced welding strategies such as pulsed MIG welding or modified environment welding can additionally aid minimize porosity concerns.
An additional additional reading innovative option entails the usage of innovative welding equipment. As an example, utilizing devices with integrated functions like waveform control and sophisticated power resources can improve weld top quality and reduce porosity threats. The implementation of automated welding systems with specific control over criteria can significantly reduce porosity problems.
Moreover, incorporating advanced monitoring and inspection modern technologies such as real-time X-ray imaging or automated ultrasonic screening can aid in finding porosity early in the welding process, allowing for immediate rehabilitative actions. On the whole, incorporating these advanced services can substantially improve porosity control and boost the total top quality of welded components.
Final Thought
Finally, understanding the science behind porosity in welding is essential for welders and makers to create high-grade welds. By determining the variables influencing porosity development and applying methods to reduce it, welders can boost the general weld quality. Advanced solutions for porosity control can better improve the welding procedure and make certain a solid and dependable weld. It is very important for welders to continually inform themselves on porosity and implement best techniques to attain optimal outcomes.